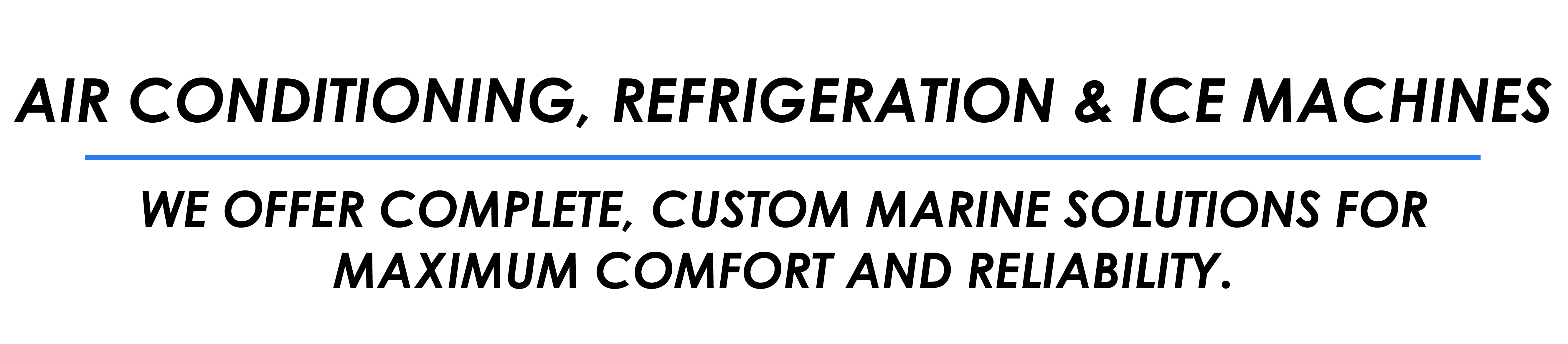
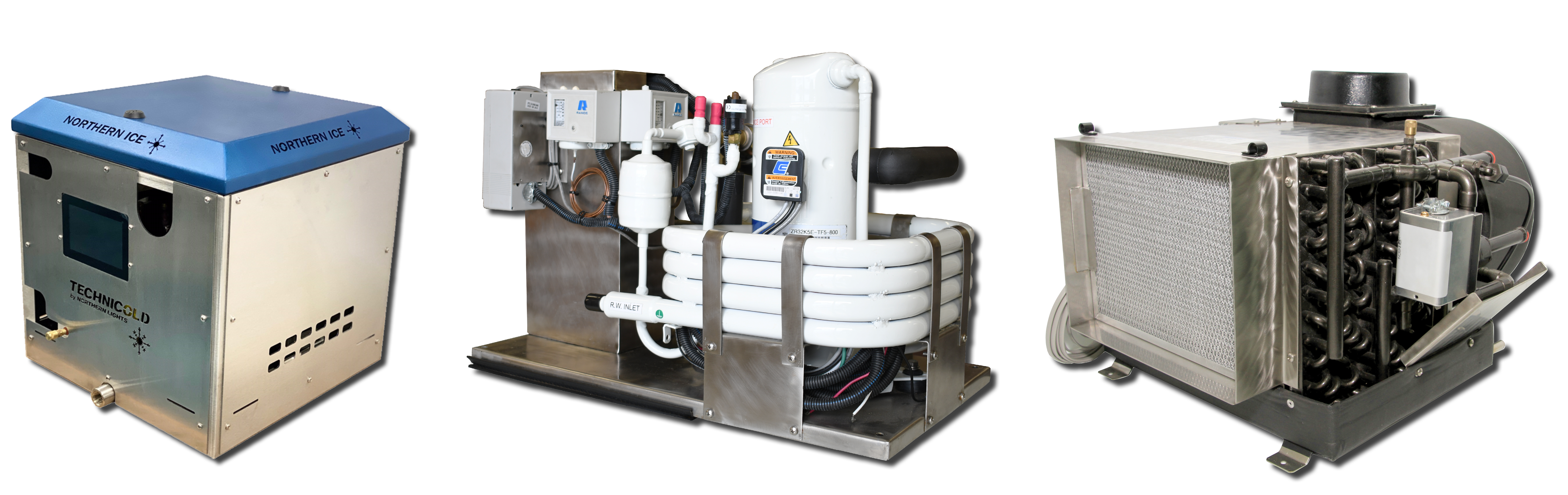
Northern Lights Marine Air Conditioners and Refrigeration products define the term “World Class”.
- Every unit uses the highest quality materials and components to ensure long life with minimal maintenance.
- Is engineered to ensure these units are compact, ultra-quiet, easy to install, and easy to maintain.
- Are perfect for applications such as Yachts, Tug Boats, Fishing Boats, Ferries, and other pleasure craft and work boats.
FAQs ABOUT MARINE HVAC SYSTEMS
There are four major considerations when shopping for a marine HVAC system. These are:
- Available space for equipment
- Available power from Generator and shore power
- Cool only or will you require heat, and how often
- Consider labor and additional materials for installation
How do I know what type of AC equipment to use? How do I determine what size AC system I need?
The first thing you must do is determine the heat load. It is important to make sure you do not underestimate or overestimate the amount of cooling power you need for your new marine AC system. This should be considered for all AC systems, including chilled water as well as direct expansion split HVAC units.
- If you underestimate the amount of BTU’s needed, you will be very hot, humid, uncomfortable, and unhappy with your system. Overestimating, or “oversizing” your AC system will lead to “short cycling”, where the AC system doesn’t have enough time to properly remove the humidity of the vessel. This will leave cold, damp air in the cooled areas.
- The general rule of thumb for choosing the proper marine AC system for your vessel is 14 BTU’s per cubic foot of air-conditioned space.
- If it is an area that is used often during mid-day, and where lots of sunlight comes in, it may be best to use 16 to 19 BTU’s per cubic foot or more.
- For areas below deck, if you only use your vessel in the evening hours, or if your boat is covered / out of the sun before entering, you can usually use 10 – 12 BTUs.
- We recommend working directly with your Marine HVAC dealer and ourselves so we can have them size the correct system components.
What is the difference between Direct Expansion and Chilled Water?
Direct Expansion (DX) This system will have a condensing unit and a separate evaporator with blower and fan coil. These two components are connected with insulated refrigerant lines. Most installations will have the condensing unit in an engine room or machinery space away from sleeping quarters. The evaporator will be placed in the area requiring the cooling/heating. The evaporator will require ducting to discharge conditioned air into the space.
DX systems are reliable and easily serviced. These systems are found most often on applications with 5 or less separate areas that need conditioned air. This means you must have space for 5 separate condensing units in the machinery space of the vessel. If there are more areas it may be time to look at a chilled water system.
Chilled Water (CW) This is an optimal AC system for larger vessels with several independent areas requiring conditioned air. Chilled water systems have water chillers installed in the machinery space that circulate chilled water to air handlers throughout the vessel. The chillers are normally staged with 2 or more units that make up the BTU requirement for the entire vessel. Multiple stages keep the chilled water circulating loop temperature low enough to absorb the heat. As the load lessens at night the BTUs required will reduce to a level that a single chiller may be enough to cool the loop water.
The major benefits of having a chilled water system are that they provide maximum performance with space savings in the machinery areas. Each air handler is controlled separately with a thermostat specific to that room and there is no limitation of how many air handlers you can have in a system or the distance between each air handler.
How does a chilled water system work?
The marine chiller circulates cold freshwater through pipes throughout the vessel, feeding air handlers in each space cooling or heating cabins quietly and efficiently. Vessels that can accommodate a marine chiller greatly benefit from space saving, energy-efficient, high-performing system. With total zone control allowing cooling and heating of different areas at the same time. Electric heat strips in the air handlers or immersion heat are available.
A marine chiller system consists of:
- The chiller assembly. Multiple stages to cool as required as heat load changes.
- Air handlers installed throughout the vessel.
- Chilled freshwater circulating piping connecting the chiller to the air handlers.
The chiller consists of typical AC components: the compressor, condenser, and evaporator. The chiller is charged with environmentally safe refrigerant which circulates throughout these components.
The air handlers consist of a blower fan and a coil. Freshwater circulates back and forth between the chiller and the air handlers through insulated piping. The water circulates through the chiller, where the heat is transferred to the refrigerant in the evaporator, cooling the water again. The heated refrigerant is the chiller’s condenser coil, and the heat is discharged via the raw water system overboard.
Both chilled water and direct expansion systems work on the same refrigeration cycle theory.
When cooling, warm cabin air is drawn (or blown) across the air handler fan coil by the blower. Heat is removed from the room air as it passes through the coil, and then cool air is blown back in. The fan coil will have chilled water in it if the system is a chilled water system. The fan coil will have refrigerant in it if it is a direct expansion system. The heat drawn from the room is then carried by the piping back to the condenser. The heat transfers from the “heated” refrigerant to the raw water and pumped overboard. This is where the heat “goes.”